Traceability and product integrity
With our traceability and product integrity system, we make a positive impact on our stakeholders by building trust and a transparent supply chain. Through our standards, we pave the way to the creation of new, state-of-the-art standards within our industry. However, Vion might cause a potential negative impact should we fail to comply with laws, regulations and voluntary standards, or through incorrect product information. In 2022, we again had no compliance issues involving product integrity.Trust in food depends on having a high degree of transparency. Connecting farmers and consumers through specific supply chains is a good way of showing people who is behind the production of their food. This gives the farmer and his or her family a recognisable face, and shows consumers that our food’s supply chain is a work of craftsmanship, from farmer to butcher or from vegan-food producer.
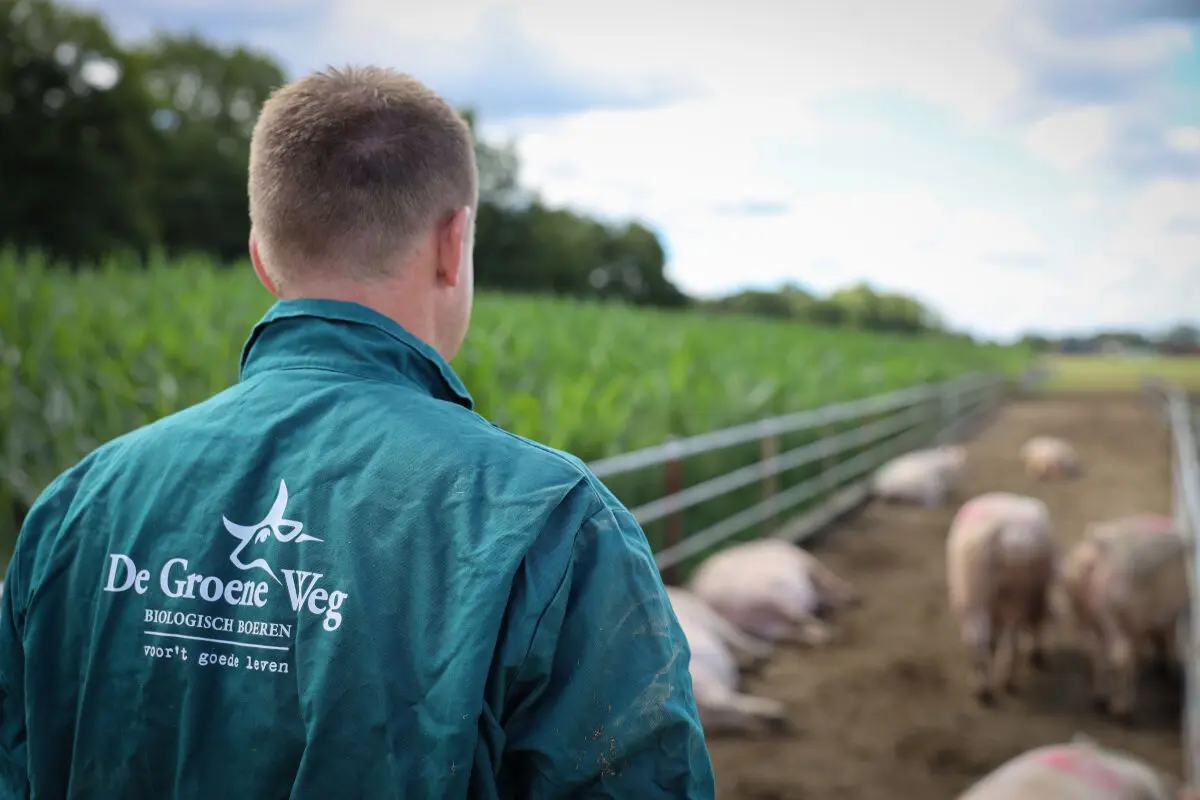
We are committed to being transparent about product origin, which we achieve by providing full traceability. Traceability information for all plant products and other non-animal ingredients processed at Vion is documented and delivered with the product, either on paper or digitally. Animals are individually marked using, for example, ear tags for cattle or tattooed number for pigs. The underlying databases enable us to trace all slaughtered pigs and cattle to their places of birth.
Following meat inspection, all carcasses are given an individual identifier linked to the ear tag, tattoo number or an RFID chip. When carcasses or parts of the carcass are processed, typical batch specifications include the processing site, slaughter site, origin of the animal, quality programmes, breeds and production dates. Relevant information is included on the consumer packaging labels, which offers the consumer guidance when making their choices. The consumer product is always traceable to a group of farmers in the supply chain.
We can trace all meats and processed products to the day of slaughter. For the processing plants, where we slaughter up to 4,000 cattle or up to 20,000 pigs a day, this means we can immediately trace, on a daily basis, the product to the group of farms which delivered the animals. For retailers and similar customers, we provide a traceability code on the package that shows the farm that supplies that specific retailer. This allows the consumer to scan a QR code. Doing so then enables them to see where the product was produced, at which plant the animal was slaughtered and when this took place.
Our quality standard includes a description of our physical and administrative processes. We make a product integrity risk assessment. This assessment results in the identification and quantification of the various risks related to product integrity. This then forms the basis for the control programme for product integrity within Vion. Part of this control programme involves the monitoring and verification of all procedures which concern product integrity. In addition, the product integrity control programme is subject to an internal peer review audit, second-party audits carried out by our customers, and third- party audits carried out by independent, accredited certification bodies.
As with food safety and animal welfare, we recognise that product integrity is primarily the responsibility of all supply chain partners. Based on this, we began to develop a Dutch Chain of Custody standard for pork, certified under the ‘Beter Leven’ standard of the Dutch animal welfare trust. This was launched in 2015 with the retail-wide introduction of ‘Beter Leven’ pork in the Netherlands. This Chain of Custody standard was developed with the Dutch Retail Association and several certifying bodies.